Group Leader
Team
Dr. rer. nat. Sandipan Sen
Raja Jothi Vikram, PhD (fellow of the AvH Foundation)
Shubhashis Dixit, PhD
M.Sc. Marcel Münch (LGF scholar)
M.Sc. Liu Yang (CSC scholar)
M.Sc. Gabriely Falcão
M.Eng. Jan Lars Riedel (head of the Materialography Lab, joint member with Fatigue)
M.Sc. Sri Rathinamani Ramdoss
M.Sc. Amin Radi
Dr.-Ing. Alexander Kauffmann (guest, Ruhr University Bochum)
We get support by our APT experts at KNMF:
Dr.-Ing. Michael Eusterholz
M.Sc. Moritz Ludwig
Research Mission
The Physical Metallurgy group focuses on the development of metallic and intermetallic materials for extreme application conditions. The identification of suitable alloy compositions and tailoring of the microstructures is particular aim of our work.
The investigation and optimization of materials for engines operating at high temperatures is of central interest. Outstanding high temperature stability (mechanical and microstructural) in conjunction with reasonable toughness at room temperature as well as suitable oxidation resistance are the main objectives in this case. Furthermore, other extreme application conditions became relevant over time, for example deformation at cryogenic temperatures close to 0 K. The research activities all have the identification of fundamental mechanisms of the important phenomena, their relationship to materials properties and application to materials tailoring in common. In order to address these objectives, we routinely apply various materials synthesis techniques and scale-bridging characterization methods.
Synthesis of New Materials
The synthesis of new materials is based on the following methods that are available in house:
- cast metallurgy: arc melter and zone melting
- powder metallurgy: attritor grinding mill, planetary ball mill, hot uniaxial pressing
- heat treatments in various atmospheres
Characterization Methods
The characterization of mechanical and thermo-physical properties as well as microstructure of metallic and intermetallic materials is performed by means of:
- standard metallographic procedures
- mechanical testing under various loading conditions (tension, compression, cyclic, creep conditions, various atmospheres)
- thermal analysis: thermogravimetry (TGA) and differential scanning calorimetry (DSC)
- focused ion beam (FIB) for microscopic preparation
- analytical scanning electron microscopy: energy-dispersive X-ray spectroscopy (EDX) and electron backscatter diffraction (EBSD)
- X-ray diffraction (XRD)
- 3D atom probe tomography (APT)
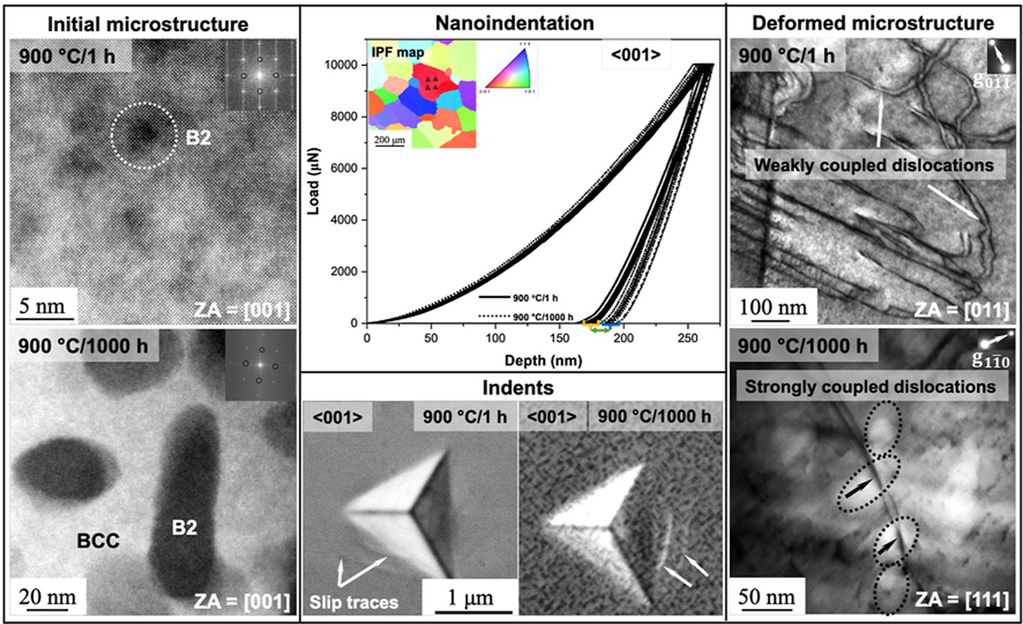
In a collaborative study with PhM, the Extreme Environments Materials Group (EEMG) at Indian Institute of Science (IISc) has conducted detailed transmission electron microscopy (TEM) investigations on aged A2+B2 precipitation-strengthened 27.3Ta–27.3Mo–27.3Ti–8Cr–10Al (at.%). At a small relative difference in lattice parameters of about + (0.6 ± 0.4) %, ageing for 1000 h leads to elongated precipitates (80 ± 16) nm in length, (26 ± 4) nm in width, and (0.25 ± 0.05) in volume fraction. The precipitates remain coherent. Nanoindentation at room temperature with subsequent TEM provided insights to the interaction of paired 1/2⟨111⟩ dislocations with B2 precipitates. By ageing, the interaction changes from weakly coupled dislocations to strongly coupled with the associated change in the precipitation strengthening contribution.
to Materials Science and Engineering A
While we have previously shown that Al-containing refractory high entropy alloys in some cases exhibit extraordinary oxidation resistance and also perform well with respect the creep resistance, the Al addition can lead to B2 crystallographic order. This is often deleterious to ductility. As B2 compounds are not generally brittle but can exhibit ductility, our collaborative work with Prof. Inui's lab at Kyoto University is dedicated to the microplasticity and operative slip systems in a model, high entropy B2 compound with the composition 27.3Ta-27.3Mo-27.3Ti-8Cr-10Al (in at.%). We confirm the activation of <111> slip directions with {110} slip planes being dominant in a wide orientation range. Additionally, {112} was verified as active slip planes for large ±χ angles. Thus, the number of slip systems is not restricted in this particular compound, but high yield strength might contribute to the embrittlement at ambient temperature. We thank Prof. Inui and his group for their incredible support and hosting Stephan Laube during his postdoc stay in Japan which was supported by the Deutsche Forschungsgemeinschaft (DFG) - German Research Foundation's priority programme SPP 2006, Compositionally Complex Alloys – High Entropy Alloys (CCA-HEA).

Refractory compositionally complex alloys consisting of a disordered A2 matrix and ordered B2 precipitates mimic the microstructures of state-of-the-art, Ni-based superalloys with A1 matrix and L12 precipitates. The former are promising candidates for high-temperature applications because of their high solidus temperatures. 27.3Ta-27.3Mo-27.3Ti-8Cr-10Al (in at. %, TMT-8Cr-10Al) is a relevant example from our group where this A2-B2, two-phase microstructure is formed by a precipitation reaction and remains stable even at temperatures close to the precipitate solvus temperature (TS). The present study systematically addresses the creep response of polycrystalline TMT-8Cr-10Al at temperatures of 1000°C and above. Compared to polycrystalline, single-phase A2 and B2 high entropy alloys, a substantially higher compression creep resistance is observed for the two-phase alloy while minimum creep rates comparable to those of state-of-the-art single-crystalline A1-L12 CMSX-4 are found. This is specifically remarkable considering the polycrystalline condition of TMT-8Cr-10Al, the open matrix A2 crystal structure and the close proximity of the test temperatures to the solvus temperature with 0.98 TS compared to 0.85 TS for CMSX-4. Consistent with a positive lattice misfit, directional coarsening of precipitates in TMT-8Cr-10Al is noted to be perpendicular to the compression direction after creep in grains with close to the compression direction.
to Acta Materialia_rdax_1024x682_98s.jpg)
On 20th and 21st of February, IAM-WK was serving to be the host of this year’s German Society for Materials Science (Deutsche Gesellschaft für Materialkunde e.V., DGM) expert committee meeting on intermetallic phases, chaired by Prof. Florian Pyczak and Prof. Manja Krüger.
The meeting covered recent advances in various materials groups:
- Mo-based and V-based silicide alloys
- Refractory high entropy alloys
- Titanium aluminides
- BCC superalloys
as well as a wide range of phenomena:
- Phase formation
- Mechanical properties, strength, creep, ductility
- Oxidation
We thank Daniel Schliephake and PhM for taking care of the organization at IAM-WK.
to the webpage of the expert committee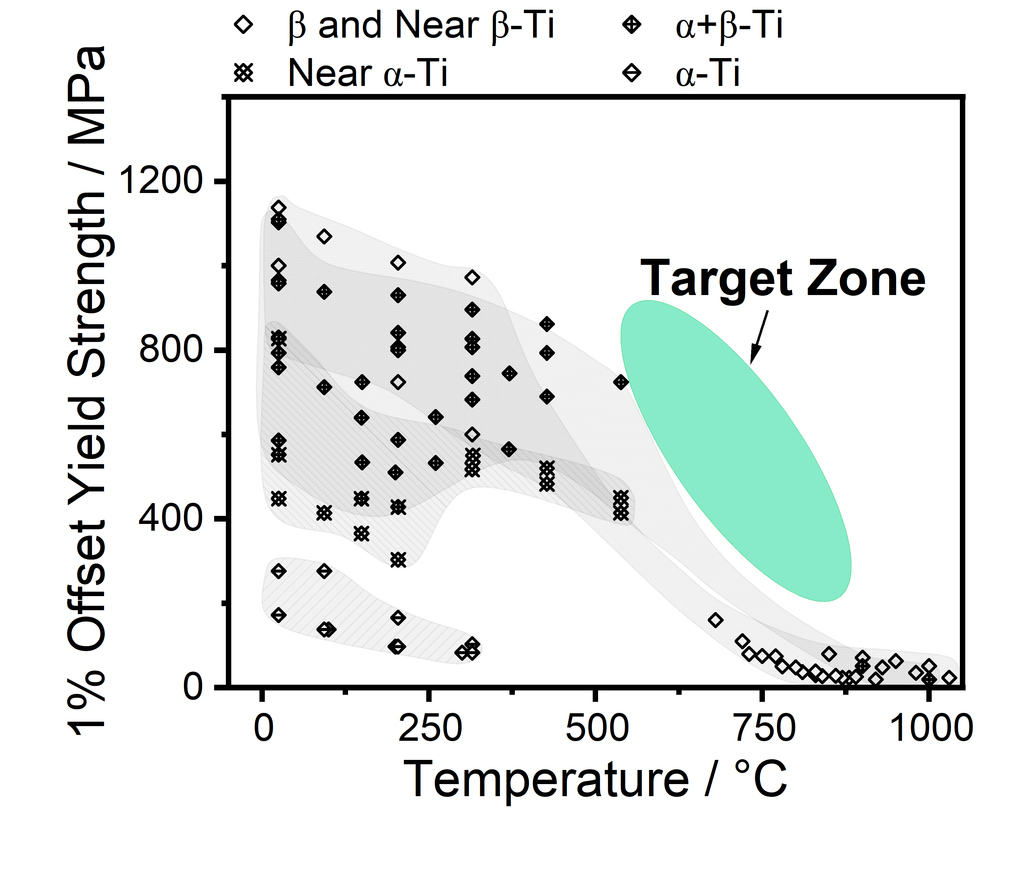
The aerospace industry demands materials that can withstand increasingly extreme temperatures while maintaining structural integrity. This project focuses on developing a novel Si-containing, Ti-based refractory high entropy alloy (RHEA) with a density of 6.1-6.4 (g/cm3) for high-temperature aerospace applications, such as jet engine compressor blades. This research aims to address the growing need for light alloys capable of operating at temperatures exceeding 600 °C, a crucial requirement for enhancing jet engine performance and efficiency. The Master's thesis aims to comprehensively investigate compression mechanical behavior of newly designed alloys and establishing understanding of the correlation between their microstructural characteristics and the resulting mechanical properties.
Contact: M.Sc. Amin Radi
Start: March 1st, 2025
Program: Mechanical Engineering or Materials Science and Engineering
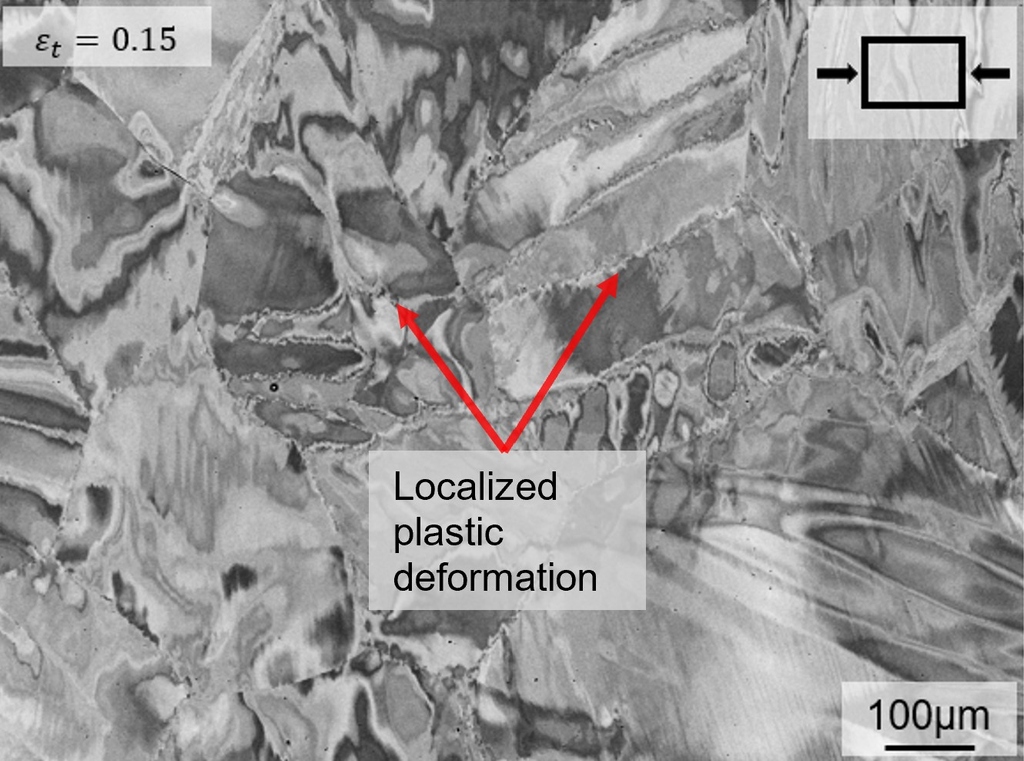
Iron aluminides are promising candidates for replacing Ni-based superalloys in certain application scenarios due to their low density and outstanding corrosion and sulfidation resistance. However, strength in single-phase condition is low at room temperature, the brittle-to-ductile transition temperature (BDTT) is strongly dependent on composition and mechanical properties are significantly influenced by point defects. Until this day, the microstrcuture to mechanical properties correlations in these materials are not fully understood. The master thesis will contribute to an improved understanding of the composition dpeendence of the BDTT.
Contact: M.Eng. Jan Lars Riedel, ILIAS announcement
Start: June 1st, 2025
Program: Mechanical Engineering or Materials Science and Engineering




Digitalization and Research Data Management
In order to address the increasing complexity of materials development and to increase the efficiency of materials characterization, our entire research activity is digitally documented in kadi4mat. We focus on documentation of complex synthesis from various raw materials and using several processing steps. Also materials characterization is recorded in detail. By contributions of Daniel Schliephake, Georg Winkens, Marcel Münch and Stephan Laube, we established the following framework:
- Research Structure
- Synthesis
- Processing
- Preparation
- Analysis
- Mechanical Testing
- Calibration
Furthermore, we make our research data publicly available along with our journal articles. In case, this did not take place, please do not hesitate to contact us for exchange of the research data.